Corrosion is a big enemy, as certain materials can be affected by environmental effects, which can cause direct and indirect problems and damages. Therefore, corrosion protection must receive the attention it deserves. In this article, we explore this topic.
What is corrosion?
Corrosion is a chemical process that occurs on metal surfaces and other materials when exposed to the environment. This natural effect has direct and indirect consequences. The direct impact is that the damage caused by corrosion leads to the need to replace parts of the equipment, which has a financial burden. The indirect consequence is the disruption of operations due to the necessary repairs. This is considered a time burden.
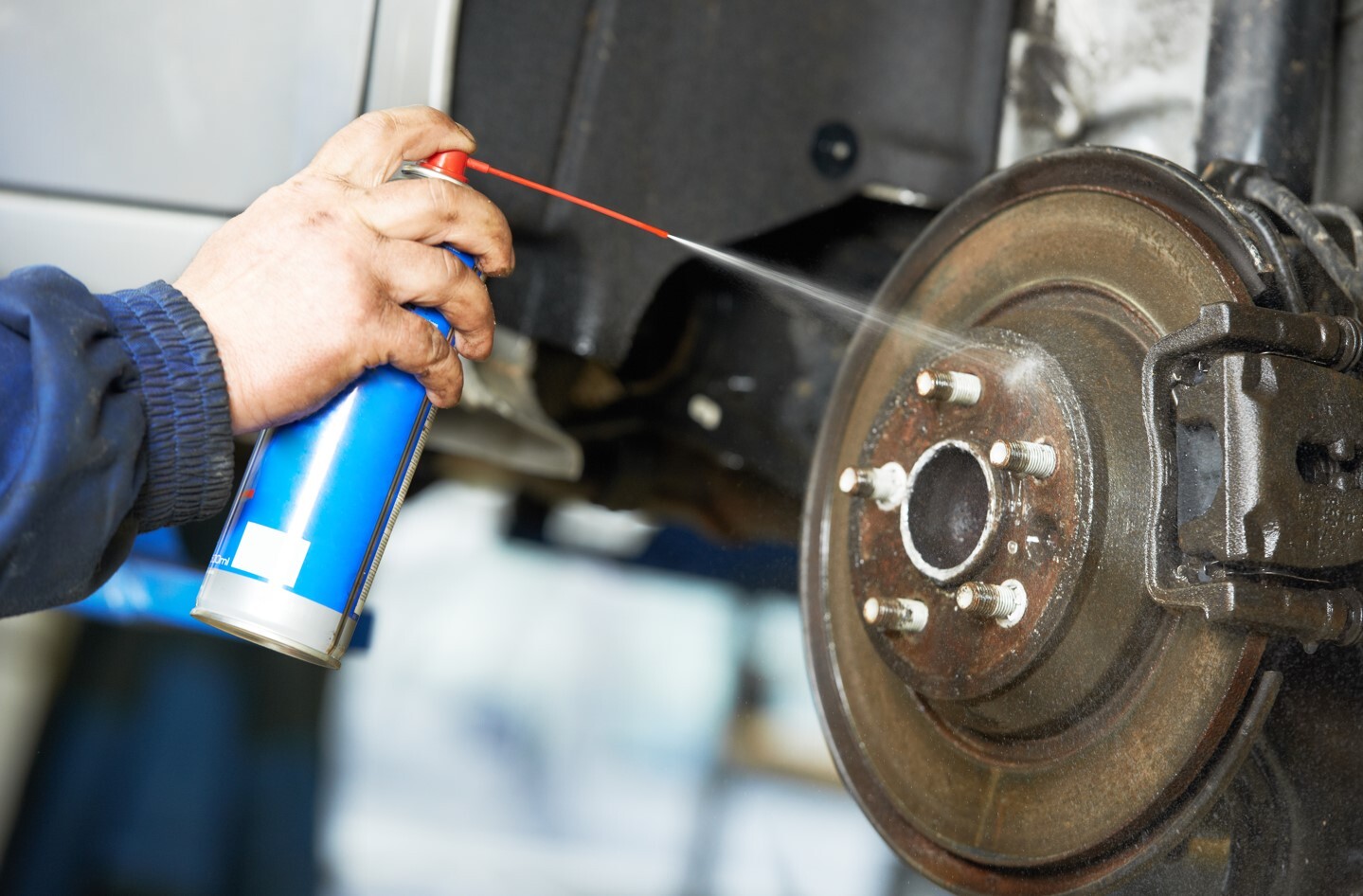
Corrosion is caused by moisture. As there is less dissolved oxygen under the water droplet, rust is formed from the ions present. Consequently, corrosion starts forming. Corrosion thus is usually triggered by natural phenomena such as humidity or precipitation.
Forms of corrosion
The corrosion process can take several forms, which are described below. Let's see what types of corrosion there are.
- Uniform corrosion: in this case, the loss of material is uniform, and the underlying cause is typically chemical corrosion or electrolytic dissolution.
- Pitting corrosion: pitting corrosion appears locally, in the form of small pits. It is most often found in humid environments or defects in protective coatings.
- Galvanic corrosion: occurs due to the non-homogeneous nature of metals as a result of environmental influences.
- Crevice corrosion: this phenomenon occurs when high tensile stresses occur in addition to the corrosion effect.
- Fretting corrosion: this type of corrosion occurs when frictional, abrasive forces are applied to the surface. Typical occurrences are rivet joints, screw joints, hinges, and joints.
- Filiform corrosion: this type of corrosion occurs under surfaces that have been painted or coated. Defects in the protection allow water to interfere, thereby causing corrosion below the layer.
Corrosion protection technologies
There are several ways to protect surfaces. Let's look at them!
Use of corrosion-resistant materials
A common method of corrosion protection is to use chemically stable materials that resist corrosion. Examples include the following materials:
Precious metals: Precious metals such as gold, platinum and iridium are well tolerant of environmental influences, but silver, rhodium and ruthenium can be sensitive to certain substances. As the price is quite high, they are mostly used as coatings.
Titanium: Titanium is resistant to corrosion and is therefore used as a structural material, coating and alloying material.
Metal alloys: alloying is used to make different metals more resistant to corrosion. Examples include stainless steel, acid-resistant steel and brass-copper alloys.
non-metallic materials: porcelain, silicon rubber and quartz glass are also popular.
The special design of the structure
Corrosion protection starts at the design stage of the metal structure, with the most important corrosion protection aspects to be considered. All elements must be accessible so that mandatory maintenance can be carried out easily.
Structures that have no or few corners are much less vulnerable to the damaging effects of corrosion. Care should also be taken to ensure that surfaces that are joined to concrete and that closed sections are sealed airtight. Particular attention should be paid to corrosion protection where the elements are fairly thin.
Forming protective coatings
There are two main aspects to consider when designing coatings: what you want to coat and what the conditions are. You need to think about the conditions in which the structure will be used, the material, the quality of the surface, the type of bonding, the intended service life and how long the structure will be expected to last. In terms of the coating, the function it will perform, the means available to form the coating and the climatic conditions at the time of construction are all important.
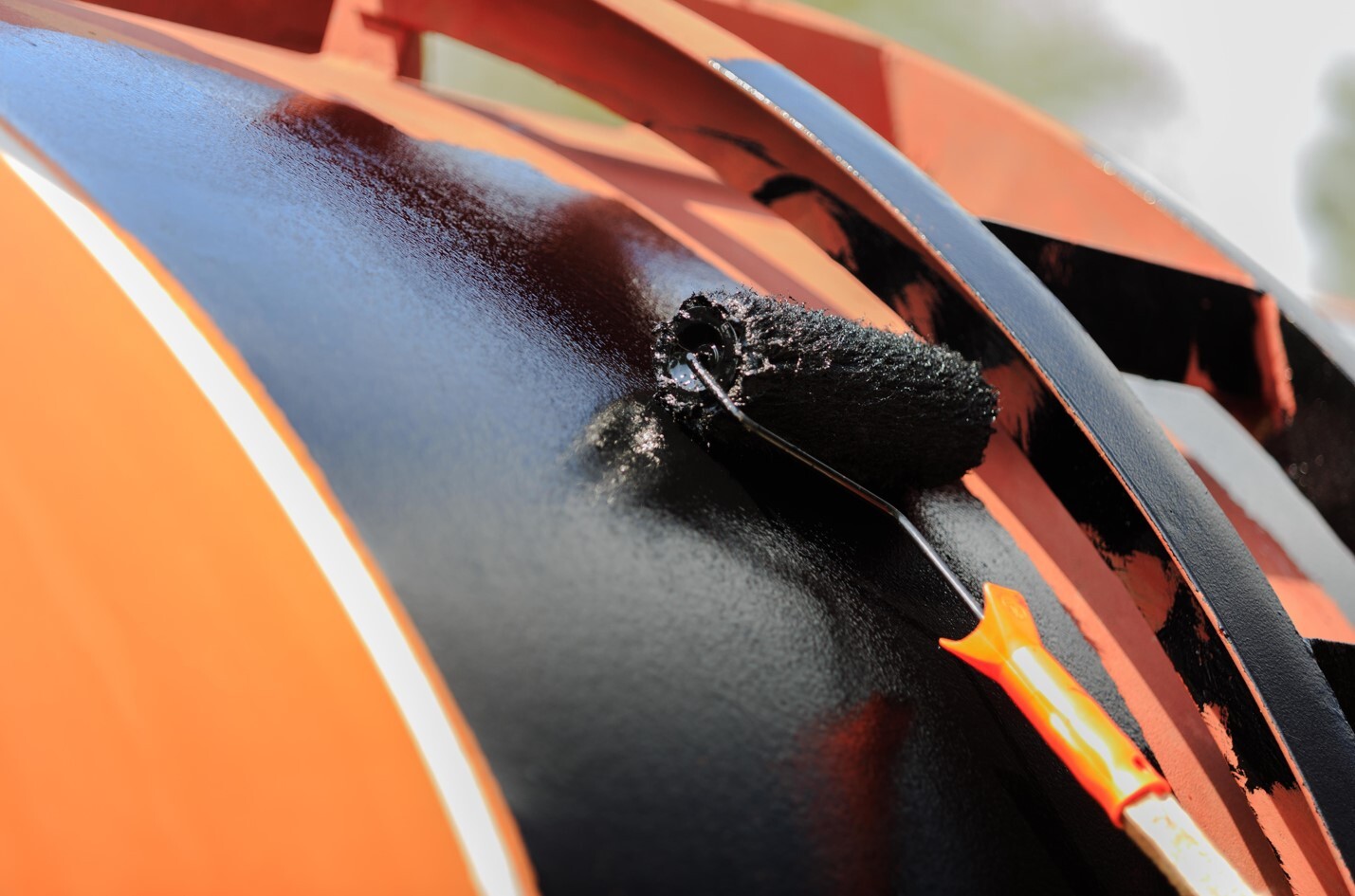
The following coatings and coating systems can be used for preventive purposes:
- hot-dip galvanising: hot-dip galvanising, is mainly used for light steel structures.
- paint coatings: these can be primer coats and coating layers. The former provides corrosion protection and the latter gives the appearance.
- combined coating systems: they have the advantage that the de-oxidation process can be omitted, but they are more expensive than the previous solutions.
A prerequisite for the application of the coating is that the surface is dry and free of contamination. It is fortunate if the air temperature is within 3 degrees Celsius of the dew point and the equipment used is suitable and has been stored properly.
Coatings can be applied in a variety of ways, such as by painting, roller, brush or spraying, using different specialised materials. Care should be taken to ensure that the drying time between coats is observed and that different coloured coats are used to ensure traceability.
Coatings can be very diverse depending on the application. For example, there are wind turbine blade protective coatings, but also coatings that are specifically fuel resistant.
Cathodic protection
The essence of cathodic protection is that the structural potential of the metal in the metal-electrolyte system is changed in the negative direction so that the rate of corrosion can be reduced by DC polarisation. It creates a galvanic current through the oxidising medium, the electron surplus of which renders the surface inert to the corrosive material.
Flanker is an online store for industry players, where customers can find everything from work safety equipment to adhesives and abrasives. Click and browse our web catalogue!