Sanding is generally considered an unpopular activity, but that doesn't mean you can get away with it. It is an activity involving a lot of dirt and is designed to remove surface irregularities. However, it is not all the same what material you use and exactly how you do it. Let's look at the properties of abrasives and what you need to know about them!
The importance of sanding
Sanding is a cutting process that removes surface roughness, improving the quality of the surface by making it suitable for a wide range of uses. Sanding can be done by hand or with a sanding machine, but the main aspect is the sanding material itself.
Sanding may be necessary for all sectors, especially where the use of metal, wood and glass is paramount. Sanding requires the right skills and experience with multiple surfaces, as thanks to advances in technology, it is possible to buy special sanding discs for different materials, thus ensuring that the quality of the sanding is good and that no damage is done to the material.
However, it is not enough to choose the right abrasive, you also need to pay attention to the grinding pressure, the cutting speed, and the feed rate to achieve the right result.
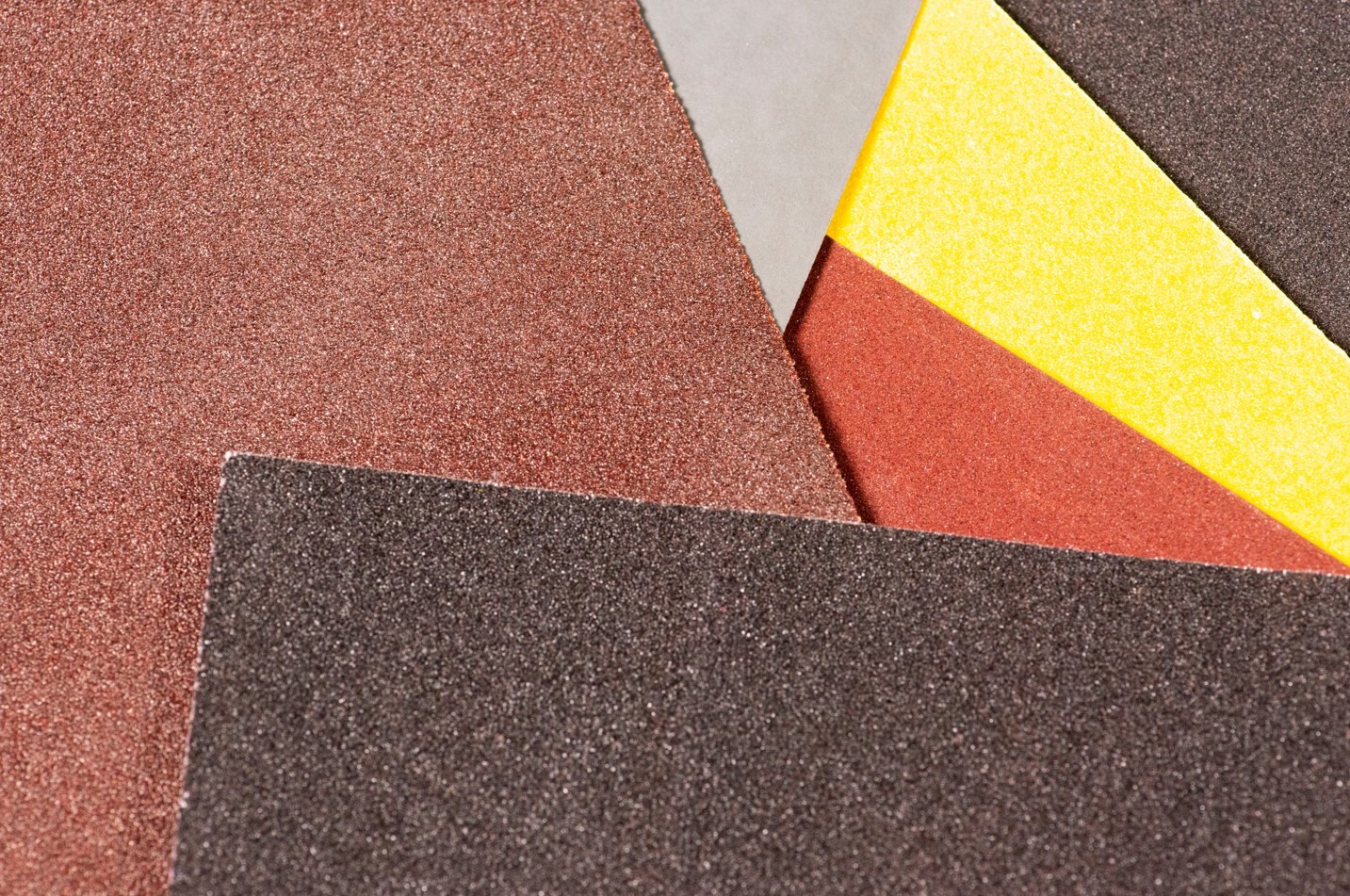
Properties of abrasives
The properties of abrasives determine the applications for which they can be used. Their structure is very simple, usually consisting of a carrier material, a binder, and abrasive particles. Let's look at them!
The carrier material
The function of the substrate is to provide a base for the grains, which is why it must withstand the various mechanical stresses, pulling, bending, and repetitive and dynamic movements. Typically, the following materials are chosen as substrates:
- paper, which can be denoted by the letters A, B, C, D and E, based on g/m2,
- fabric, denoted by X, XF, YX, J and JF,
- vulcanised fibre, which can be denoted by thickness as V8 and V6,
- foil.
The popularity of paper carriers is high. Paper carriers are very reasonably priced, but not so strapacious, and are therefore mainly used for flat grinding. Tissue backings are stronger than paper and are therefore well suited to processes such as abrasive stripping or profile sanding using abrasive belts. Vulcanized fibre, or fibre material, is made of cotton and cellulose fibres. This type is used only and exclusively for fibre discs. Finally, the foil is a thin layer of polyester, best used when fine sanding is done with discs or belts.
The binder
The bonding agent ensures that all abrasive particles adhere to the surface of the substrate and do not detach from it. It must therefore provide sufficient strength, yet still, allow for elastic movement of the grains. Resin is the most suitable material for this purpose, but natural adhesives may also be used as a bonding agent.
The abrasive grain
Abrasive grit can be made from a variety of materials, including corundum, zirconia-corundum, ceramics, silicon carbide and diamond. The following is an overview of the types of grit that can be used to grind which materials:
- Ruby: this is a natural abrasive grit with a hardness grade of 7-7.5 on the Mohs scale.
- Smirgel: this is a harder (7.5-9) but natural grain, like Ruby. It is used for grinding non-ferrous metals and precious metals.
- Cycron corundum: cycron corundum is a synthetic material with a hardness grade of 9. It is used for grinding minerals, CK (cement-bonded chips), and steel.
- Brown corundum: also a synthetic material, brown corundum has a hardness grade of 9.
- Semi-precious corundum: reinforcing the corundum camp, it is a synthetic material used for grinding wood and metal.
- White corundum: white corundum has a hardness of 9,4 and is used for sanding wood, paint and varnish.
- Silicon carbide: silicon carbide with a hardness grade of 9,3-9,7 is widely used for grinding glass, stone and MDF.
- Diamond: the strongest abrasive grit is diamond, suitable for grinding glass, marble and ceramics.
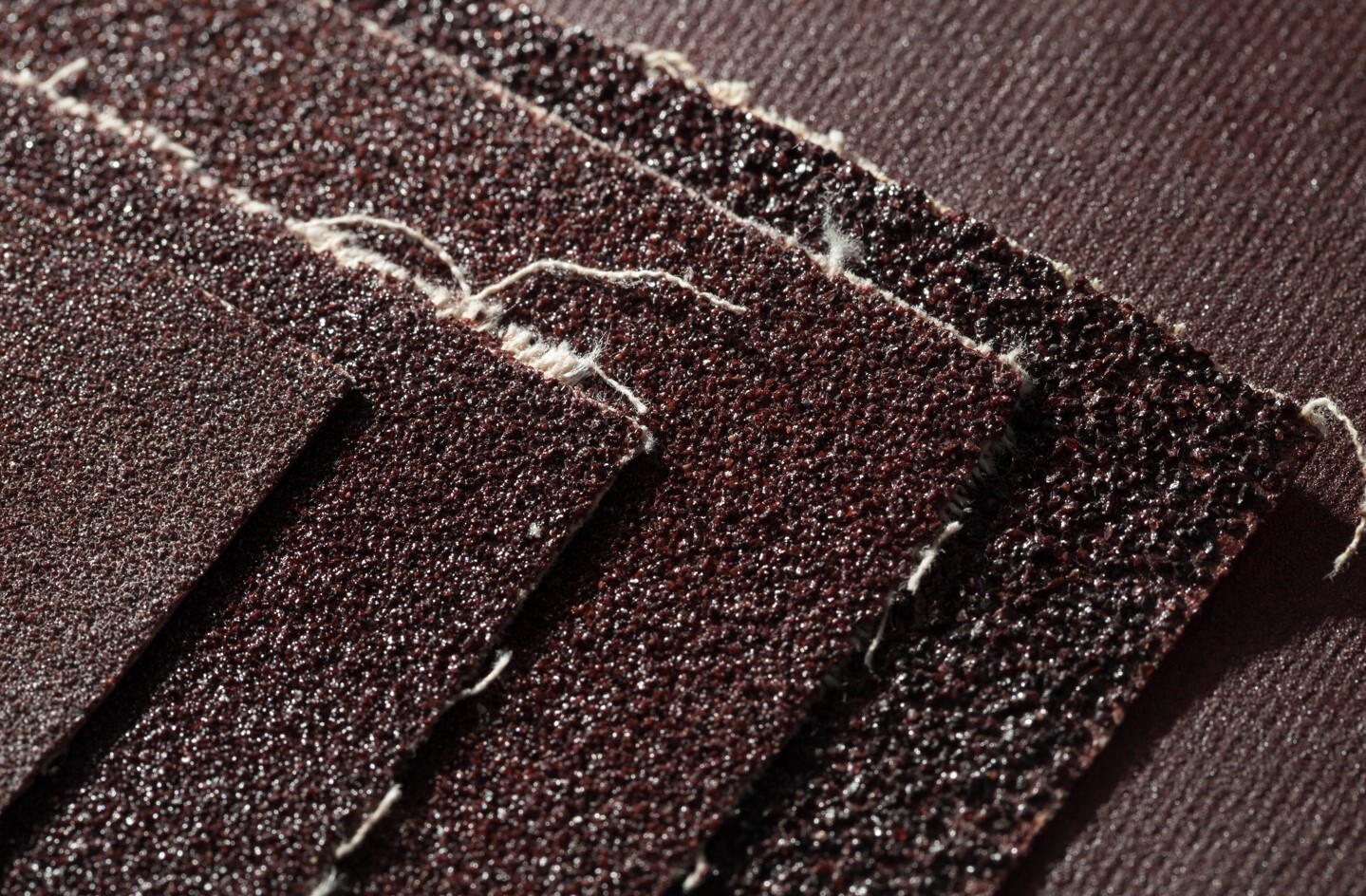
It is also important how the grains are positioned on the substrate, i.e. how the grains are distributed. With open grit, the grains are less frequently spaced, allowing the dust generated during grinding to settle temporarily between the grains. This is advantageous because it prevents dust from remaining on the surface. With closed grit, the grains are more densely spaced, which means that there are more of them and therefore more cutting edges. While open grit abrasives are recommended for softer materials, closed grit abrasives are recommended for harder materials.
The higher the value, the smaller and finer the grain. In the process, it is, therefore, advisable to use a coarser grit for pre-sanding, followed by an intermediate grit, and finally a fine grit for finishing.
The abrasive varies according to the application. There are, for example, sanding sponges, sanding belts, sandpaper, sanding rollers and sanding discs for machines.