Adhesives play a vital role in many industries by bonding materials effectively and permanently. Hence, the hot melt applicator is a key tool for precise adhesive dispensing. This blog post aims to introduce the types, functions and applications of applicators to give you an overview of these tools. Let's get started!
Hot melt applicators are tools used to apply various adhesives to various surfaces smoothly. They are ideal for industrial environments where pressure and accurate dispensing are key. Dispensing guns are used by many industries as they allow accurate dispensing and efficient work.
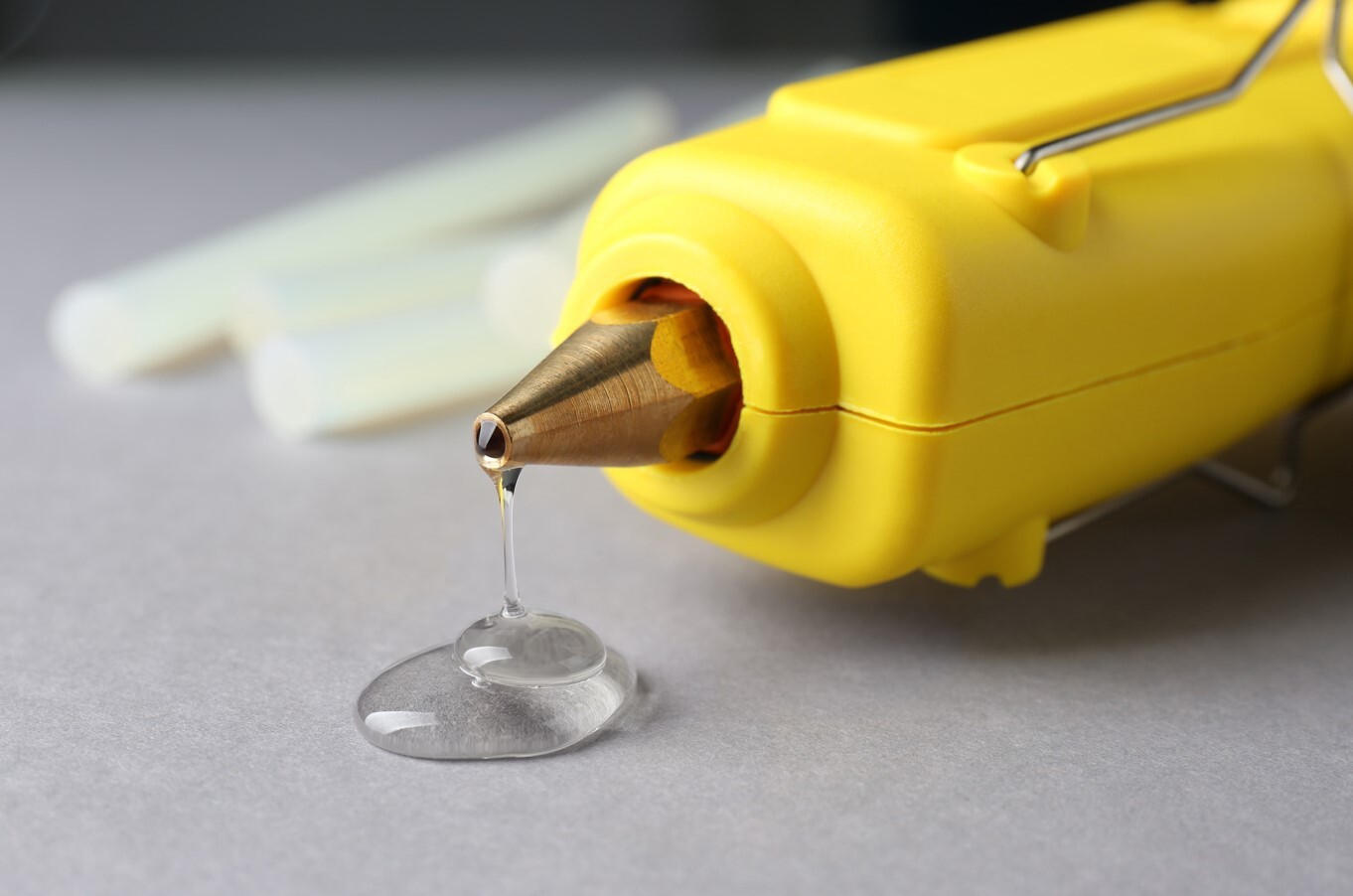
Types of applicators
Manual applicators
Manual applicators are popular for smaller jobs. They are simple in design, delivering the adhesive to the surface via a manually operated lever. They are quick and easy to use, especially where mobility and flexibility are required.
They have the advantage of being available at a low cost and do not require an external power source. In addition, their ergonomic design makes them comfortable to use. However, they have the disadvantage that the application of pressure is limited, which can be tiring for the worker when applying large quantities of adhesive.
Pneumatic applicators
Pneumatic applicators operate with air pressure, which allows continuous and even dispensing. They are ideal for industrial environments where high volumes of work and precise dispensing are required.
Pneumatic applicators have the advantage of providing a high-pressure force so that even denser adhesives can be applied to the surface. An example of such a dispenser is the 3M 8012 pneumatic applicator.
Hot melt applicators
These applicators use hot melt adhesives which are heated and dispensed in a liquid state. The 3M Hot Melt EC, 3M Hot Melt PG II, 3M Hot Melt PG LT Quadrack and Low Melt TC Quadrack are adapted to different applications and temperature requirements.
They have the advantage of fast curing and strong adhesion, making them ideal for fast work. They have a variety of nozzles that allow precise dispensing of the adhesive. The disadvantage is that the high temperature of the hot melt adhesives can be potentially dangerous for the operator, so appropriate protective equipment must be used.
Electronic dispensing guns
Electronic dispensing guns use advanced technology to dispense adhesive. These devices can be precisely controlled, which is an advantage in complex industrial applications. Different manufacturers' specifications allow the selection of the appropriate type.
Technological details include adjustable temperature control and automatic pressure control, which allows for uniform adhesive dispensing.
The advantages are high precision and minimal waste. Disadvantages are that they are available at a higher price and may require more maintenance than mechanical devices.
Applications and Industries
Printing and paper industry
Applicators are a key tool for the printing and paper industry, providing high accuracy and uniform adhesive application. Precise glueing is essential in this industry, especially when it comes to ensuring a perfect bond between thin papers and fine materials. Applicators make the glueing process quick and easy, greatly increasing productivity and reducing the possibility of errors.
Hot melt guns are most used in the printing and paper industry. These guns heat the adhesive quickly and allow for immediate use, which is particularly important in high-volume production processes.
Packaging industry
Efficiency and precision are at the forefront of the packaging industry's requirements. Uniform and accurate glueing minimises waste and ensures that packages are securely sealed.
Hot melt applicators are particularly popular in this industry, ensuring continuous and reliable adhesive application.
In addition, pneumatic dispensing guns are also common, as they can apply adhesives at higher speeds and with less manpower.
Automotive industry
Bonding processes in the automotive industry are complex and often require high-strength bonds. Applicators play a key role here too, particularly in the assembly of body panels and interior accessories. The adhesives used require high heat and pressure resistance, so applicators also need to be robust and reliable.
Pneumatic applicators are often used in this industry, especially when glueing structural components such as windscreens. Such applicators provide high-precision adhesive application, which is of paramount importance in maintaining the safety of vehicles.
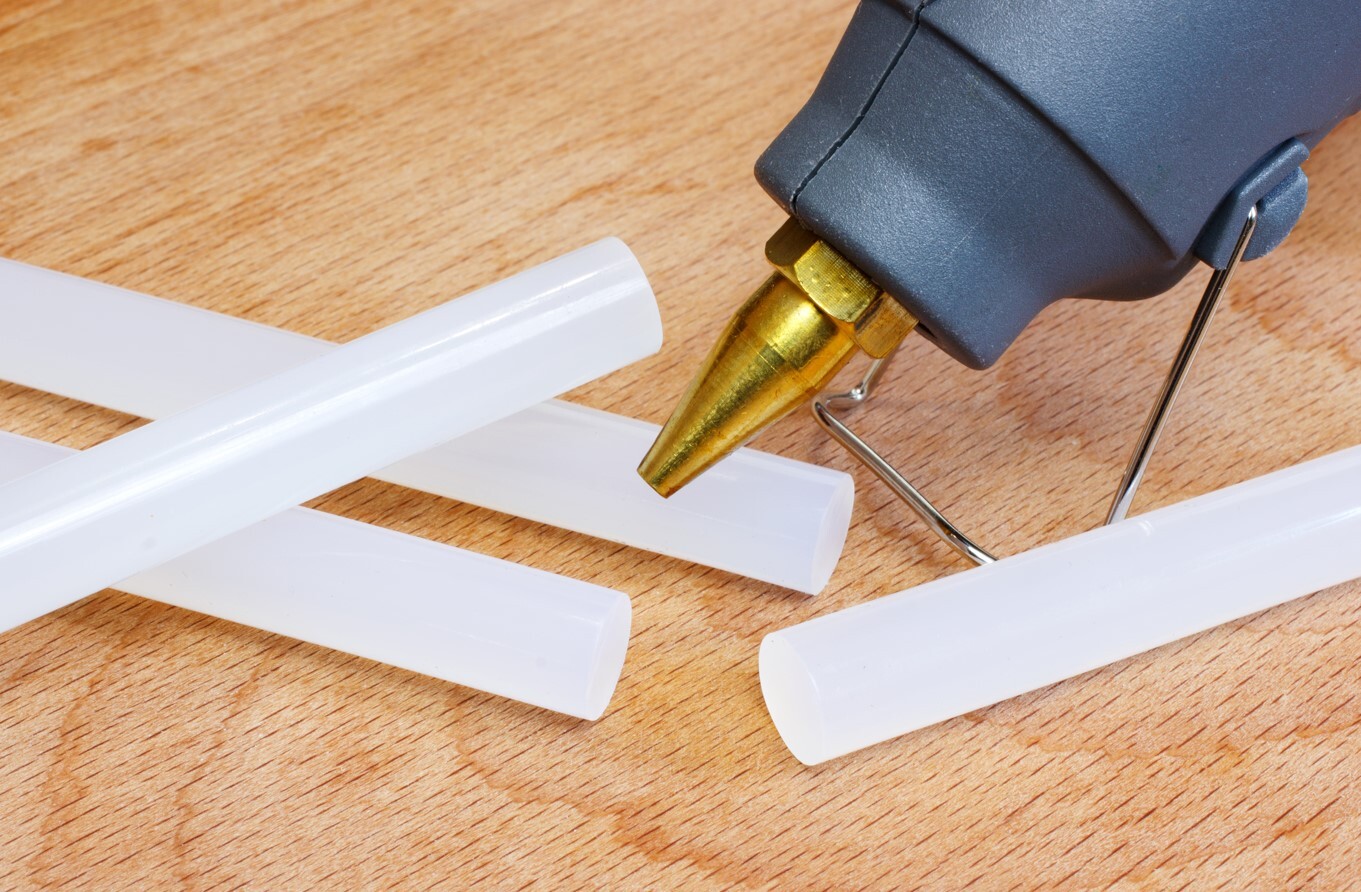
Electronics industry
In electronics manufacturing, applicators must meet specific requirements. The joining of tiny, precise components requires extreme care and precision. The adhesives used here stand out not only for their bonding strength but also for their electrical insulation properties.
Furniture manufacturing and ship maintenance
In furniture manufacturing and ship maintenance, the use of applicators makes it easier to join different materials such as wood, metal and plastic. Bonding with applicators results in fast and secure bonding, which increases the efficiency of the manufacturing process and the quality of the products.
Find the right tools at Flanker! We offer a wide range of adhesive applicators for all your needs!